10:14 pm
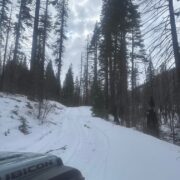

Club President
April 2, 2003

Never even knew they existed!
I have a 1310/1350 combo joint on the lower end of my DL. Guess what failed? Yup, the 1310 parts.
It only cost me $40 to upgrade to the full 1350 rear with the larger yoke and joint. They didn't have the yoke today so I am still running the combo joing until I can bring the DL back in this winter to get the work done. I need to check the front DL while I'm at it.
I wonder if these are common and place like Autozone carry spares.
11:32 pm


Club Member
September 3, 2008

3:44 am
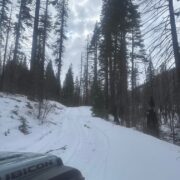

Club President
April 2, 2003

3:32 pm

January 27, 2011

1:56 am

"LJ3" wrote: I have the same thing on my jeep. just didnt want to pay for new drivelines when i upgraded the axles so 1310 to 1350 for now and i carry 2 spairs u-joints just in case.
When Brads u-joint failed, it ripped the drive shaft yoke apart. The crack started before this run and progressed slowly until it snapped. I'll be bring the pieces to the meeting. If you're a hard wheeler, you might want to consider installing a new 1310 every year or so and use the old one for a spare.
8:47 am

"Bender" wrote: [quote="RockinCrawler"]The crack started before this run and progressed slowly until it snapped.
What makes you think that?
Because there are about 2-3 visible chevron marks. On the side near his ring finger. Crack started there and progressively opened/closed, until finally overload (Oh Snap) and it pops. Large piece failure on the side near his index finger.
3:49 pm

Not sure I see any sort of evidence of "progressive cracking" from the pictures either. It'll be interesting to see it in person. It's tough for me to imagine a load on a u-joint that would cause it to last long after cracking. Especially with no noticeable vibration and since it lasted through more than one hop when he broke it. Maybe it deflected on the first hop and broke on the second?
7:32 pm
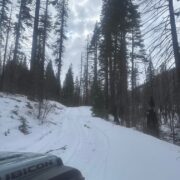

Club President
April 2, 2003

I too am unsure of the progressive cracking theory simply because of the damage. I doubt a severely weakened end would have torn the drive line ears off. I think it would have just caused the U-joint to fail.
Also, the others side tore off as well.
Only the 1310 ears sheared off. Neither of the 1350 ends showed any damage.
5:19 am

Cyclic loading i.e., fatigue is the root cause of the failed trunnion on the ujoint. The beach marks (rings) are the tell tale evidence of a fatigue failure. A crack can start from anything really or was already present with a defect in the trunnion. It just takes a certain load to activate it or other contributing factors. For example, the needle bearing could have started a wear line. Btw, how old is that ujoint, just for kicks?
The crack was propagating until it experienced overload, which is classic shear failure mode. In this hardened steel, the smoother surface is the propagating crack side. It's a more uniform texture relative the shear side (lumped material). This is classic brittle fracture to ductile shear tearing. Pretty great stuff and such a fundamental case to have on hand really.
It's expected that the 1310 side would fail since it more than 10% reduced in size. I suspect the yoke flange got ripped off simply from the trunnion being bound up.
Lastly, I would guess these ujoints are used for flexibility in driveshaft/axle shaft combinations, high angles, and/or purposely engineering a weak point in the line. If you're going to break something, break something that you can fix on the trail.
Apologies for my .02
2:39 pm
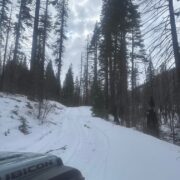

Club President
April 2, 2003

2:47 pm

Still not sure I buy it as a fatigue failure. To be clear, fatigue isn’t an area of expertise for me so I'm working on a gut feeling and barely enough knowledge in the subject matter to be dangerous. Fortunately, I have a close friend that that does a lot of this sort of thing. I sent him the pictures for giggles. Here’s a summary from him. Again, neither of us have actually seen the piece, but his last offer is certainly interesting in a geeky sort of way. 😀
"Materials Enginerd" wrote: Well, first off, it’s hard to see the “beach” marks on a fatigue failure (unless it’s very high stress & low cycle…and then it’s arguable when that becomes static overload) without magnification. I don’t see any in this picture. Second a fatigue failure usually looks like concentric thumb prints emanating outward from a failure origin which would be on the outside diameter, not the inside diameter...which, if I am looking at the right “rings” they are going the wrong way for a fatigue failure staring at the surface.
Even though it doesn’t quite look like fatigue it also looks like it was broken for a while prior to the overload. The picture is crummy, so I can’t see much on the clean facet which is the newest portion of the failure. To be honest it looks more like a defect than anything…i.e. it had some voids at the casting level so it was doomed to fail.
But..I can’t tell for sure without the actual piece or a better picture… mail me the nub and I’ll take it to our failure analysis lab…it’s just a hobby for me
Brad, any idea what brand it was?
3:22 pm

Had a problem with 1310"s a while back. +/- 2 years The trunnions were going away in as little as 50 miles of street driving. Was found by re-greasing after a short distance. The red amsoil grease was turning black ish on some trunnions. The shop made some calls to the mfg. and others had been having problems also. The shop replaced all joints F & R of both jeeps and our spare rear ds with ones of a different lot number. Have not had an issue to date. Maybe Brad's was from the same era. Brand was spicer.
4:35 pm

"Bender" wrote: Still not sure I buy it as a fatigue failure. To be clear, fatigue isn’t an area of expertise for me so I'm working on a gut feeling and barely enough knowledge in the subject matter to be dangerous. Fortunately, I have a close friend that that does a lot of this sort of thing. I sent him the pictures for giggles. Here’s a summary from him. Again, neither of us have actually seen the piece, but his last offer is certainly interesting in a geeky sort of way. 😀
[quote="Materials Enginerd"]Well, first off, it’s hard to see the “beach” marks on a fatigue failure (unless it’s very high stress & low cycle…and then it’s arguable when that becomes static overload) without magnification. I don’t see any in this picture. Second a fatigue failure usually looks like concentric thumb prints emanating outward from a failure origin which would be on the outside diameter, not the inside diameter...which, if I am looking at the right “rings” they are going the wrong way for a fatigue failure staring at the surface.
Even though it doesn’t quite look like fatigue it also looks like it was broken for a while prior to the overload. The picture is crummy, so I can’t see much on the clean facet which is the newest portion of the failure. To be honest it looks more like a defect than anything…i.e. it had some voids at the casting level so it was doomed to fail.
But..I can’t tell for sure without the actual piece or a better picture… mail me the nub and I’ll take it to our failure analysis lab…it’s just a hobby for me
Brad, any idea what brand it was?
My degree is Materials Engineering with an emphasis on Welding. Failure analysis is the game, just as your friend rolls around in. In his defense, the pictures are not the greatest and that having in hand with good scopes, this can be better assessed. However, being there right when it happened, the beach marks were much more evident. Course, I'm not sure where the indication of stating failure as at the inside diameter....
Figured I wouldn't need to thrust a background about given the detail I provided (or rationale) for this type of failure mode. Meh....this is 50/50 internet and RL though.
I did read the follow on posts.
I'm curious...is the combination joint in Jeeps just common all the way around, regardless of setup (stock to extreme)?
1 Guest(s)

